Ft System`s innovative design for high frequency fill level inspection
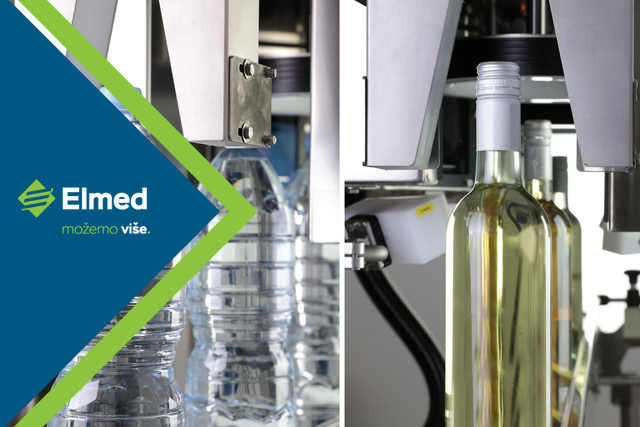
Smaller footprint and greater versatility to more easily embed fill level inspection into filling machines.
A major engineering study conducted by FT System highlights strong innovative elements in the wine, spirits and beverage market reagrding the high-frequency fill level inspection used for accurate level measurement - even in foamy beverages (e.g. beer or CO2 drinks). This was discussed with Eng. Andrea Arturi, member of FT System’s standardization team, who is involved in innovating existing inspection machines in line with customer and market needs.
The standardization team of FT System’s technical office has put forward significant innovations for the high-frequency fill level inspection machine. What aspects have you worked on?
First, let me reiterate once again that the accuracy and precision features of FT System’s high-frequency fill level inspection have remained unchanged. We’ve mainly focused on footprint through an engineering study which was jointly developed and shared with the leading machine manufacturers that FT System builds strong collaborative relationships with.
The project was created to respond to new market needs, including embedding fill level inspection directly into the filler monobloc, with the two-fold advantage of saving space in the manufacturing sites, as well as avoiding waste compared to more downstream fill level inspection systems. Also, the reduced footprint makes it possible for us to more easily process different types of bottle formats, from standard to mignon, both inside fillers and as standalone equipment.
How did you achieve the goal of reducing the footprint of high frequency level control? What criteria did you follow?
Our industrialization project started with the analysis of the single mechanical and electronic parts that make up this type of machine. With a view to reducing footprint, we carried out accurate market research on single parts in order to come up with solutions that could take up less space while ensuring identical or even higher performance. The electrical boards, for example, were replaced by smaller ones, and so were other mechanical parts such as the analyser head and its columns. The result was a 40% reduction in the footprint of the high-frequency fill level inspection system; as a result, the current overall dimensions are 285x245x90 (WxHxD,) referring to the complete inspection head without support. This makes it possible to embed fill level inspection into a monobloc machine more easily, regardless of the size of the processed formats. This makes FT System even more competitive on the market and able to meet the different fill level inspection requirements of wine, spirits and beverage manufacturers.
Did you explore any other significant issues in your engineering project?
Hygienic design guidelines are a standard for us, from the choice of materials through to design. The other issue is the complete washability of the fill level inspection system to be embedded into the monobloc machine - a feature increasingly sought after by companies to reduce cleaning and sanitation times for their manufacturing lines. By leveraging attention to small details and meticulously working on the machine’s features, we have succeeded in achieving our goal - a machine that can be easily incorporated into our customers’ manufacturing lines, boasting a footprint that is today among the smallest on the market, with minimal bottle-size-related restrictions.