Palletizing cobot for the food industry with imaging systems can be used in cramped spaces
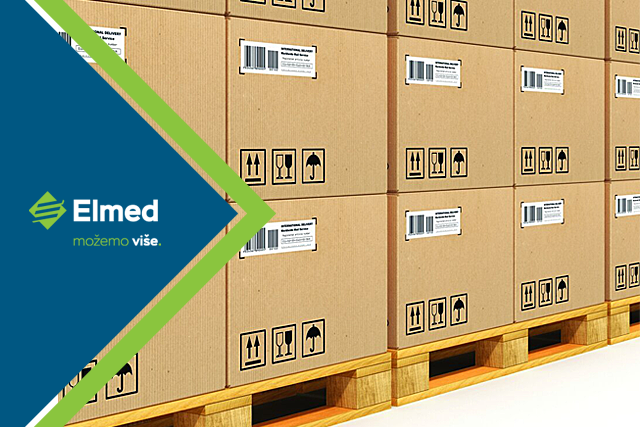
In short:
The Norwegian meat producer Nortura needed to optimize the palletizing, but had limited floor space and a fixed budget. A UR10 robot with a ceiling-mounted imaging system provided a cost-effective, high-performance palletizing system on one-fifth of the area normally required. If there are no pallets, the floor surface can be used for other processes.
Challenge:
Typical palletizing robots require a large fixed cell with a guardrail that takes up a lot of floor space. Nortura wanted to be able to palletize continuously without stopping the production line, but had a need to be able to use the surface for other processes if there were no pallets.
With its limited budget, Nortura had another challenge in finding a cost-effective 6-axis robot with the range and payload capacity needed to stack boxes of different sizes and weights on a pallet. The robot also needed to be flexible and easy to program to work with the imaging system and reliable enough to run with minimal monitoring.
Solution:
Nortura wanted to optimize the palletizing, but could not use a traditional palletizing robot that requires a large permanent cell with a guardrail. . The IFM O2D222 image camera is mounted in the ceiling above the robot, which is mounted under it on a narrow stand and is equipped with Unigripper SMS 80-200 vacuum holder. When the robot is in sleep mode, the mounted robot only takes up a floor area of 0.5 m 2. The robot's work area is simply a painted surface on the floor that marks where the operator should place an empty stool. "We used maybe 10 to 20 percent of the area that a traditional robot would have used," says Lars Bårdgard Åstveit, developer at Rocketfarm AS. “When there is no stool there, the surface is empty; it is as if the palletizing system did not exist ”.
When an empty pallet is placed on the floor, the imaging system automatically detects both it and boxes that come on the conveyor belt and start palletizing by themselves. "No one needs to tell the robot that there is a box here, so start palletizing it", Åstveit adds. "The system itself sees it and begins to palletize". The program for the robot with 6 arms can be easily adapted to stacking boxes in different sizes as requested by the customer, such as to turn the drawers so that the drawer labels are visible from all sides of the pallet. The robot can stack an average of 20 pallets every day, ie a total of 1,700 boxes per day.
An additional advantage is that the robot can provide fault control for the previous machines on the production line. While people may not notice that a box has not been filled properly, the robot weighs each box and signals if a box with fewer packages inside arrives on the line. "UR10 is a robot that has all the right specifications", stated Åstveit. "It is cheap, has the range that not many other cobots have and it has the payload that allows it to lift the products we need to lift. And it is quite flexible in its programming ”.
But the most important aspect was its ability to work safely next to people. The UR10 robot automatically stops if it runs into something that is not part of the planned path, even if it is a human standing on an empty stool. "If it could not do that, we would not have been able to use this robot," said Åstveit. “It is an important function and it decided the deal. Without UR10's security function, we would not have been able to do this job ”.
Nortura estimates that the payback period for the palletizing system is less than one year if it is run in one shift, and it is possible to run more shifts if needed for an even shorter payback period. Nortura were actually so happy with the system that they immediately ordered two more systems to be run on other production lines that will go even faster with smaller boxes.